
Registration Open
Morning Breakfasts In Networking Exhibition Area

Chairs Opening Remarks

Innovative Thermal Management Solutions For Electric Vehicle Batteries: Multi-Functional Heating And Cooling Systems
As the demand for electric vehicles (EVs) continues to surge, the efficiency and longevity of EV batteries have become paramount. Central to this is the development of advanced thermal management systems that can effectively regulate battery temperature. This presentation delves into multi-functional thermal heating and cooling systems, highlighting their critical role in optimizing battery performance, safety, and lifespan. Attendees will gain insights into the latest technologies, design strategies, and future trends in EV battery thermal management.
-
Components of Multi-Functional Thermal Systems: Overview of heating and cooling mechanisms; integration of phase change materials (PCMs) and liquid cooling systems; role of advanced materials in thermal regulation
-
Technologies in Focus: Heat pumps and thermoelectric coolers; passive vs. active thermal management systems; innovations in thermal interface materials (TIMs)
-
Future Trends and Developments: Emerging technologies in thermal management; potential impact of solid-state batteries on thermal systems; trends towards integration with vehicle climate control systems.

Maximizing Lithium-Ion Battery Safety: Strategies For Enhanced Performance And Reliability
Mekiyah Bailey, Field Application Engineer II, Parker Lord
-
Understand the impact of increased energy density in lithium-ion batteries on performance and longevity
-
Identify the inherent risks associated with high energy density in lithium-ion batteries, particularly thermal runaway, and its implications for EV safety
-
Explore comprehensive strategies for enhancing battery safety, including:
-
Battery cell chemistry optimization
-
Cell design improvements
-
Advanced thermal management techniques
-
Utilization of advanced materials in battery packaging
-
Implementation of sophisticated battery management systems
-
Gain insight into EV battery safety by:
-
Surveying different types of batteries commonly used in EVs and their associated hazards
-
Analyzing root causes of battery failures and identifying effective solutions for ensuring battery safety
-
Discuss effective strategies for preventing or mitigating battery thermal events, considering the importance of proactive measures in safeguarding EV drivers and passengers

Maximizing Efficiency & Unlocking Battery System Performance Whilst Driving Down Cost Of Battery Pack Production
David Brandt, Technical Sales Manager – E-Mobility, SIKA
-
Unlocking performance in your battery thermal management system utilizing state of the art gap fillers and thermally conductive adhesives
-
Enabling maximum performance whilst maintaining efficient manufacturing processes to drive down the costs of battery pack production
-
Reduce weight and improve efficiency utilizing the latest materials to market in order to meet the demands of the latest adoptions in the BEV landscape
-
Design by nature: Using nature to influence design in battery thermal management?
-
Materials: Finding the sweet-spot for thermal conductivity
-
Sustainability: How solutions can enable repair, reuse and recycling

Thermal Management Strategies For Faster Charging, Extended Range, And Propagation Prevention
Bret Trimmer, Applications Engineering Manager NeoGraf Solutions
-
Explore the challenges and opportunities as we delve into cutting-edge technologies, strategies, and best practices to optimize thermal performance in EVs
-
Review the latest goals and best current methods for EV, ePlane, eVTOL, and Maritime battery thermal management
-
Examine the five factors that allow cells to charge quickly and discuss the single factor that pack designers can control
-
Unravel the secrets to maximizing driving range through innovative thermal management materials
-
Explore the four primary strategies battery pack manufacturers use to prevent Thermal Runaway and the impact of each on fast charging, cell performance, and cell lifetime
-
For applications where smaller-pack-size and lighter weights are essential, flexible graphite will be discussed as a direct substitute for aluminum

Lightweight Battery Potting & Encapsulation Compounds For Thermal Management
John Albaugh, Market Development Manager, Electric Vehicles, Elkem ASA
This presentation will address the challenges that battery engineers face in designing lightweight battery packs that manage heat effectively. It will explore different types of potting & encapsulation compounds, such as syntactic and gas-foamed compounds, and highlight the importance of innovative materials like 3M™ Glass Bubbles. Gain a deeper understanding of these compounds and their significance in thermal management.
-
Understand key challenges in designing lightweight, thermally efficient battery packs
-
Explore various potting & encapsulation compounds, including syntactic and gas-foamed types
-
Learn the role of innovative materials like 3M™ Glass Bubbles in thermal management

Morning Networking Break
Sponsored By
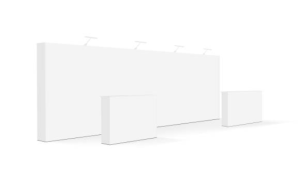

Battery Cooling: Harnessing Laser Welding For Stronger, Lighter, Sustainable Aluminum Cooling Plates
Adrian Serna, Business Development Specialist , AdvanTech International
-
Explore the advantages of laser welding, including enhanced strength, reduced weight, and cost savings, achieved through the utilization of robust yet affordable materials
-
Examine the environmental advantages of ground breaking laser welding technology, particularly in terms of reducing the CO2 footprint, and its contribution to sustainability efforts
-
Gain insight into the practical applications of laser-welded aluminum cooling plates across various industries, understanding their potential market impact and benefits
-
Analyze the trajectory of laser welding technology, forecasting its potential to reshape the landscape of battery cooling solutions and its broader implications for industrial applications

Unveiling The Power Of Technology For Enhanced Fire Protection In Electric Vehicles
Alexander Teufl, Head of Sales – Battery Protection, AIS Ltd.
-
How to increase safety against Thermal Runaway
-
How to protect against Thermal Runaway up to 250Ah per cell
-
Application know-how to optimize the module & pack production
-
Comparing different shielding technologies per application

Accelerating Battery Pack Simulations With Engineering-Focused 3D Multiphysics CFD
Jun Li, Business Development, AVL Advanced Simulation Technologies
3D Computational Fluid Dynamics (CFD) simulations play a crucial role in battery pack development by minimizing the need for physical prototypes, enhancing thermal performance, and ensuring compliance with safety and durability standards. Despite their benefits, these simulations often demand extensive effort in mesh preparation and execution due to the intricate geometries and physics involved. Join experts as we highlight various features of our 3D simulation tool designed to streamline these processes and significantly reduce turnaround time.

Processing Of Foams For Thermal Propagation Protection
Wim Dexters, Sales Engineering Director, bdtronic, Americas
-
Explore the fundamental principles underlying the generation of foams for thermal propagation protection in battery modules, including the key mechanisms involved in foam formation and their significance in preventing thermal runaway
-
Analyze various concepts and techniques for processing foams in battery applications, elucidating their individual advantages and disadvantages in terms of thermal management, adhesion, and overall performance
-
Understand the critical parameters and considerations involved in the selection and application of foaming adhesives for thermal propagation protection, including factors such as material compatibility, processing conditions, and environmental considerations
-
Assess the impact of foam processing techniques on the structural integrity and reliability of battery modules in automotive electric vehicles, highlighting best practices and potential challenges faced by battery engineers and manufacturers
-
Gain insights into innovative approaches and emerging trends in foam processing technology for thermal propagation protection, with a focus on enhancing efficiency, performance, and safety in automotive battery applications

40 Min Round Table Panel
Leveraging AI For Enhanced Thermal Management In Lithium-Ion Batteries
Moderator:
Panelists:
Artificial Intelligence (AI), particularly machine learning, is transforming thermal management in lithium-ion batteries. By integrating machine learning with first-principles calculations, researchers are gaining a deeper understanding of lithium-ion de-embedding and its effects on thermal conductivity. This technology also enhances battery temperature monitoring and prediction, improving heat dissipation, ensuring better battery performance, and preventing thermal failures.
Understand the Role of Machine Learning in Thermal Management: Explore how machine learning techniques, combined with first-principles calculations, improve understanding and management of thermal conductivity in lithium-ion batteries
Enhance Battery Temperature Monitoring: Learn about the integration of machine learning with sensors for reliable and accurate temperature estimation, leading to better battery performance and prevention of thermal failures
Improve Safety Management with Predictive Techniques: Discover how machine learning can predict operating conditions and enhance safety management in energy storage systems by effectively monitoring and analyzing battery health and safety status

Networking Lunch Break
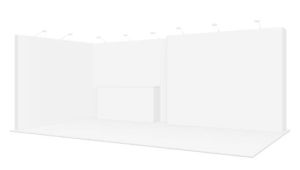

Thermal Innovations For EV Battery Safety: Unveiling Next-Gen Solutions
Dezarai Shepherd, EV Battery Innovation Lead, Stanley Black & Decker, Inc.
-
Addressing Critical Challenges in Li-Ion Batteries: Safety, performance, lifetime, costs, and sustainability, and explore how effective thermal management can mitigate these challenges
-
Understanding the Effects of Charging and Discharging Cycles: Learn about the volumetric changes, swelling, and contraction experienced by batteries, especially in prismatic cells, during charging and discharging cycles, and their implications for battery performance and safety
-
Exploring Novel Approaches in Thermal Management: Discover innovative approaches such as integrating thermal barriers with swelling compensators to address thermal propagation risks and battery cell swelling, and understand the effectiveness of these solutions through experimental investigation and numerical simulations
-
Optimizing Thermal Management Solutions: Gain insights into optimizing the use of swelling compensators and thermal barriers to effectively mitigate thermal propagation risks, leading to improved safety, performance, and longevity of EV batteries
-
Advancing Thermal and Pressure Management Strategies: Explore advanced thermal and pressure management strategies in battery packs, to enhance the safety, reliability, and efficiency of EV batteries

Technological Advancements & Latest Insights On Battery Pack Thermal Management
Nathan Saliga, Chief Engineer, One | Our Next Energy
-
Get a complete overview of advancements made in thermal management technology to cool battery packs
-
Understand the process used to develop these technologies including where they started, the current stage they are at, the challenges encountered and how they are being overcome
-
Examine new battery cell chemistries and their thermal requirements
-
Assess results from abuse testing for battery packs

Maximizing Thermal Runaway Protection With Advanced Cell-to-Cell Barriers
Cell-to-cell thermal barriers offer cutting-edge solutions for mitigating thermal runaway propagation in electric vehicle (EV) batteries. By integrating these ultrathin, lightweight barriers, battery engineers can meet stringent safety standards and enhance battery pack performance. This presentation will delve into the benefits of barriers, focusing on their ability to stop thermal propagation, perform dual roles as compression pads and fire barriers, and support next-generation cell architecture. Learn how these advanced materials can help achieve your battery safety and performance goals.
-
Understand Thermal Runaway Mitigation: Explore how thermal barriers effectively stop thermal propagation at the cell-to-cell level, enhancing overall battery safety
-
Meet and Exceed Safety Standards: Learn how these solutions help engineers satisfy critical safety requirements, including China’s GB38031 and the UN’s ECE/TRANS/180/Add.20 standards
-
Optimize Battery Pack Design and Performance: Discover how barriers support maximum volumetric cell-to-pack ratio (VCPR) and perform essential mechanical and thermal functions, leading to improved battery pack performance

Breaking The Trade-Off Between Product Quality And Development Time Using 3D Deep-Learning Algorithms: Heat Exchanger Optimization
Frederick Garrett Reis, Director of Sales for US, Neural Concept
-
Understand how predictive models based on 3D Deep Learning algorithms accurately forecast numerical simulation results in near real-time directly from 3D CAD geometry
-
Explore the capabilities of Deep Generative models in swiftly generating innovative design variations
-
Learn about fully automated optimization campaigns that efficiently optimize geometries, leveraging predictive and generative capabilities
-
Discover a powerful and open platform enabling OEMs to seamlessly integrate deep learning technology into existing workflows and effectively use it in production
-
Gain insights into recent algorithms based on Geometric Deep Learning, which enable shortcutting simulation chains through predictive models outputting post-processed simulation results and optimization suggestions directly from CAD designs
-
Implement predictive and generative models to streamline heat exchanger optimization processes, leading to significant performance enhancements
-
Understand how AI models can emulate the expertise of simulation engineers, empowering product or design engineers to make informed decisions early in the development process
-
Uncover the complexities of heat exchanger design and the advantages of utilizing AI-driven internal CFD simulations for non-parametric optimization

Enhancing Electric Vehicle Safety: Thermoplastic Thermal Runaway Barrier Solutions
Explore how innovative thermoplastic-based thermal runaway barrier solutions are revolutionizing electric vehicle (EV) safety by preventing fire spread within battery systems. Test results demonstrate the efficacy of materials in providing thermal insulation and flame resistance, reducing the risk of cell-to-cell propagation during thermal runaway scenarios. Discover how flame-retardant resins have been evaluated and verified for their ability to delay flames effectively, ensuring enhanced safety in EV battery enclosures.
-
Thermal Runaway Mitigation: Understand the role of thermoplastic-based thermal barrier solutions in mitigating thermal runaway events within EV battery systems, reducing safety risks associated with high-temperature gas, open flames, and pressure increases
-
Material Performance and Verification: Learn about the performance characteristics of resins and its ability to provide thermal insulation and flame resistance, as well as certifications for effective flame delay performance in battery enclosure applications
-
Application in EV Battery Components: Explore real-world applications of thermoplastic materials in EV battery components, including module enclosures, busbars, and end plates, and understand how these materials contribute to meeting stringent fire safety regulations and improving overall safety, efficiency, and performance of EV battery systems

Enabling Battery Circularity: Innovations In Debondable Adhesives
Discover latest advancements in debondable adhesives, designed to promote the circularity of batteries through enhanced repair, re-use, and recyclability. These innovative adhesives address the growing need for high structural integrity in high energy density battery designs, such as cell-to-pack configurations, while also facilitating the disassembly process essential for battery repair, re-use, and recycling.
-
Circularity in Battery Design: Understand the importance of debondable adhesives in enabling the circularity of batteries, allowing for efficient repair, re-use, and recycling of battery components and materials
-
Structural Integrity and Disassembly: Learn how debonding technology enhances the structural integrity of battery cells within the battery tray or vehicle structure, while also enabling seamless disassembly for maintenance, repair, and end-of-life processes
-
Sustainability and Environmental Impact: Explore the role of debondable adhesives in advancing sustainability goals by promoting the reusability and recyclability of battery systems, contributing to the reduction of waste and environmental impact associated with battery manufacturing and disposal

Afternoon Networking Break
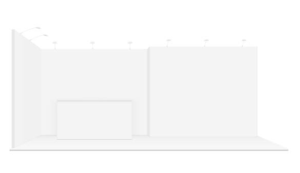

Sealing Safety: Coating Solutions For Next-Gen EV Battery Packs
Discover the advancement of Electric Vehicle (EV) development through cutting-edge solutions tailored for enhanced safety, performance, and manufacturing efficiency. From advanced battery fire protection to thermal management solutions and shielding coatings, this presentation will explore a comprehensive portfolio that addresses critical challenges in EV battery pack design and production. Gain valuable insights into innovations that are driving automotive powertrain systems.
-
Enhancing Safety and Performance: Understand how solutions for advanced battery fire protection, thermal management, and dielectric isolation coatings contribute to enhancing the safety and performance of EV battery packs, ensuring reliable operation and mitigating risks of thermal runaway
-
Streamlining Manufacturing Processes: Discover how automated application processes and coatings facilitate increased manufacturing throughput, optimizing efficiency and scalability in EV battery pack assembly
-
Collaborative Innovation: Learn about the critical challenges in EV battery pack design and production, ultimately accelerating the development of next-generation automotive powertrain systems

40 Min Round Table Panel Discussion
Seal Integrity in EVs: The Urgent Need For Testing and Industry Specifications
Moderator: Ryan Bostick, CVO, Founder, Finding Engineered
Panelists:
EV and EV Batteries need to be airtight, water tight, or even helium tight depending on the application, but the industry doesn’t have any sealing specifications, much less proper testing requirements.
-
Major areas of the vehicle from the battery cell or box to the exterior that require some level of sealant to protect from water, air, dust, or external invasions that can kill the vehicle or worst case the drive
-
What types of tests can be done in each of those scenarios from the battery pack at the OEM to the completed cell at the vendor
-
Examples how each of those applications are sealed by the vendor or OEM
-
What happens in each scenario if a seal fails from fire to catastrophic failure of the vehicle
-
Discuss the need for an industry spec and testing requirements that’s enforceable

Sealed For Success: Solutions For Immersion Cooling In EV Batteries
This presentation delves into the rising prominence of immersion cooling technology for electric vehicle (EV) batteries and the critical role of sealing systems in ensuring its safety and efficacy. Innovative materials address the challenge of leak-proofing immersion cooling systems, crucial for maintaining the integrity of coolant circulation. From sealing gaps during battery cell insertion to withstand prolonged coolant exposure, engineered compounds offer robust solutions for EV manufacturers seeking reliable immersion cooling.
-
Understand the significance of immersion cooling in enhancing EV battery efficiency and charging times
-
Explore the challenges associated with ensuring leak-proof seals in immersion cooling systems, particularly in EV batteries
-
Learn about advanced potting compounds and sealants engineered to address the unique sealing requirements of EV battery immersion cooling

Innovative Tape Solutions For Mitigating Fire Propagation Risks In Electric Vehicle Battery Systems
Join us for an insightful presentation addressing the critical challenge of maintaining optimal battery temperatures to prevent thermal runaway events. With the demand for electric vehicles rising, effective thermal management solutions are paramount to ensure safety and reliability. This session will focus on innovative tape solutions, specifically engineered to provide thermal barrier protection and prevent the spread of thermal events between battery cells. These solutions offer heat-absorbent and flame-resistant properties, along with electrical insulation, effectively reducing the risk of fire propagation within battery modules.
-
Understand the challenges faced by automakers in maintaining optimal battery temperatures to prevent thermal runaway events
-
Explore innovative tape solutions, designed to provide thermal barrier protection and mitigate the spread of thermal events between adjacent battery cells
-
Learn about the heat-absorbent, flame-resistant properties, and electrical insulation capabilities, and how they contribute to enhancing safety and reliability in electric vehicle battery systems

Chairs Closing Remarks

All-Attendee Drinks Reception

Registration Open
Morning Breakfasts In Networking Exhibition Area
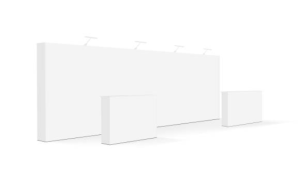

Chairs Opening Remarks

Innovative Cooling Solutions For EV Batteries: Pioneering Cell Design
A leading OEM has recently filed a patent for innovative battery cells designed to enhance cooling efficiency through unconventional shapes. Moving away from the traditional rectangular form of the current Ultium cells, the OEM proposes Lego-like shapes that create cooling channels when assembled into modules. This design aims to extend battery life by improving cooling directly over a larger surface area. However, the complexity of manufacturing these nonuniform cells presents significant challenges. This presentation will delve into the technical and production implications of this new design, evaluating its potential to revolutionize EV battery performance and production.
-
Understanding the Design Innovation: Explore the unique Lego-like shapes of these proposed battery cells and how they create cooling channels to improve thermal management and battery longevity
-
Evaluating Manufacturing Challenges: Assess the complexities and potential production challenges associated with manufacturing nonuniform battery cells
-
Projecting Future Applications and Impact: Discuss the potential impact of this innovation on the OEM’s future EV models and the broader EV market, including anticipated benefits and the feasibility of integrating these new cells into upcoming vehicle designs

Exploring The Boundaries Of Multi-Material Assembly Through Cutting-Edge Friction Welding Elements Technology
Arnaud Gug, Director of Product Management, EJOT Industrial Division
-
Learn about the crucial role of innovative fastener solutions in adapting to new multi-material battery structures and ultra-high strength steels, while maximizing lightweight materials
-
Understanding the necessity for reliable production processes capable of seamlessly integrating with diverse materials and thicknesses to meet the demands of high-volume battery manufacturing
-
Explore the game-changing benefits of a rapid and straightforward friction welding process, slashing cycle times without any surface preparation or pre-drilled holes
-
Unlock the potential of minimal heat affected zone and compact profile in friction welding, coupled with its versatility with various adhesives, revolutionizing manufacturing efficiency

Maximizing Efficiency And Sustainability In EV Battery Assembly With Plasmatreat
Frank Petrolli, VP Strategic Market Development, Plasmatreat
Alex Borchardt, Sales & Business Development, Plasmatreat
We’ll unveil the future of EV battery assembly processes, where Plasmatreat(ment) technology emerges as a revolutionary force. Prepare to be captivated by the incredible versatility of Plasmatreat(ment) as it cleans and activates surfaces, transforming automotive manufacturing. Explore a world of possibilities with over 100 diverse applications, and be amazed by its game-changing impact on production processes. Dive into the cutting-edge #OpenAirPlasma® Technology, where Plasmatreat(ment) elevates EV battery assembly, enhancing thermal management, bond strength, corrosion protection, and more. Discover how it paves the way for scalable battery production, aligning perfectly with the rapid growth of the EV industry. Join us on this eco-friendly journey, as Plasmatreat(ment) reduces VOC and CO2 emissions, championing sustainability. And, the excitement doesn’t end there – gain valuable insights into traceability and zero downtime.

Electrification: How OEMs Accelerate Architecture Research & Definition While Optimizing Power, Range, Reliability, And Cost
Anthony R. Giesey, SVP & Head of Brands, EVONOMY Group
A dynamic session where you’ll discover how more than 250+ leading OEMs are propelling the rapid development and continuous refinement of their next-generation vehicle architectures. Delve into the intricacies of optimizing power, range, reliability, and cost while staying at the forefront of innovation. Explore the Evonomy Ecosystem, supported by a network of 700+ suppliers, driving over 90% of new electrified architectures across diverse industries including Automotive, Aviation, Off-Highway, Logistics, and Marine. Gain invaluable insights from the company that has spearheaded the evolution of Automotive architectures, from 48V to extraordinary voltages like 900V and beyond, setting a precedent for innovation in various sectors. Don’t miss this opportunity to be at the forefront of cutting-edge architectural advancements.
-
Overview of this exciting Ecosystem and how it supports 95%+ of all next-generation mobility architecture
-
Learn market trends for industry adoption, including the roadmap to 10kV+ electrified powertrains & fully autonomous vehicles
-
Learn about state-of-the-art electrified powertrain, autonomous-enabling sensors, software stacks, and development tools

Unleashing The Potential: Innovations In Powder Coating For Enhanced BEV Component Performance
Kevin Hales, Automotive Innovation Manager – Powder Coatings, Akzonobel
Uncover the transformative power of powder coating in battery electric vehicle components. Explore the remarkable advancements, applications, performance enhancements, and environmental benefits that powder coating offers in BEV components. Gain valuable insights into the unique challenges faced when powder coating BEV components, from intricate designs to material requirements, as we tackle these challenges head-on to achieve flawless results. Discover the future trends and emerging opportunities in the rapidly evolving field of powder coating for BEV components, setting the stage for new horizons in innovation.
Delve into the critical role of powder coating as a protective insulating layer for battery packs, mitigating the risk of electrical system failures and preventing heat build-up in batteries, ensuring optimal safety and performance. Unlock the secrets behind powder coating’s exceptional electrical insulation properties, empowering even the most intricate designs with high dielectric strength, extraordinary adhesion performance, and exceptional thermal shock resistance. Unlocking the untapped potential of powder coating for enhanced BEV component performance.

Morning Network Break
Sponsored By
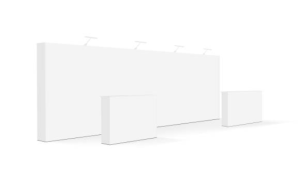

Innovative Joining And Sealing Solutions Achieved By Flowform® Fasteners And PIAS® Nuts For Electric Vehicle (EV) Battery Manufacturing
Thomas Klama, Application Engineer, ARNOLD Fastening Systems, Inc.
Joerg Pecho, Director Functional Parts Pre-Series Production, ARNOLD Fastening Systems, Inc.
Explore the pivotal role of comprehensive joining solutions in battery design and manufacturing processes within the context of today’s electric vehicle landscape. This session delves into the use of Flowform® fasteners and PIAS® Pierce nuts to build robust, leak-free battery packs, safeguarding them from environmental factors. Discover innovative approaches for tackling joining challenges across various material stack- ups, adhesive applications, and sealing methods for battery housing designs.

Improved Methods For Leak Testing Lithium-Ion Batteries
Ryan Takacs, Sales Manager, Zeltwanger
Highlighting the critical importance of Battery Leak Testing for ensuring both safety and performance in the field of battery technology. Delving into comprehensive test solutions spanning from laboratory settings to the production scale within Giga factories, covering a spectrum of battery components, including cells, modules, packs, enclosures (trays and lids), cooling channels, and associated components. The presentation underscores the pivotal role that rigorous leak testing plays in safeguarding battery systems and maximizing their efficiency at various stages of development and production.

Digital Twin Of EV Batteries: A Cradle-To-Grave Solution For Streamlining Development, Production, And Disassembly
Katharina Gerber, Engagement Lead – Battery Industry, Siemens Digital Industries Software
The Digital Twin of an EV Battery serves as a comprehensive cradle-to-grave tool, optimizing every stage of the battery lifecycle—from initial design to end-of-life disassembly. Starting with the optimization of cell design, this digital model allows for the precise integration of cells into modules and packs, incorporating simulations for thermal runaway events, thermal management, optimized cooling strategies, and Battery Management Systems (BMS). This holistic approach enables developers to refine designs and anticipate performance under various conditions. Beyond the development phase, the Digital Twin provides valuable support during the production process by generating detailed bills of materials and bills of manufacturing. It streamlines assembly by offering a virtual guide, ensuring accuracy and efficiency. As the battery reaches the end of its life, the Digital Twin becomes a critical asset for sustainable practices, providing a blueprint for the automated disassembly of used EV packs. It serves as an instructional document for robotic systems, enabling efficient recycling and recovery of valuable materials. This comprehensive digital approach not only enhances the development and testing phases but also ensures a sustainable and cost-effective end-of-life process for EV batteries.
Optimization of Cell Design and Integration:
-
The Digital Twin starts by optimizing the design of individual cells and their integration into modules and packs
-
Simulations for thermal runaway events, thermal management, optimized cooling, and Battery Management Systems (BMS) are incorporated to enhance safety and performance
Support for Production and Assembly:
-
Provides detailed bills of materials (BOM) and bills of manufacturing (BOMfg) to streamline the production process
-
Offers a virtual guide to ensure accurate and efficient assembly of battery components
End-of-Life Management and Disassembly:
-
Acts as a blueprint for the automated disassembly of used EV battery packs
-
Serves as an instructional document for robotic systems to efficiently recycle and recover valuable materials
Holistic Lifecycle Approach:
-
Enhances every stage of the battery lifecycle, from initial development to sustainable end-of-life management
-
Ensures a cost-effective and environmentally friendly approach to EV battery production and recycling

Navigating Global Regulatory Requirements For Thermal Propagation
Rich Byczek, Global Technical Director, Transportation Technologies, Intertek
Thermal propagation testing and performance have been key challenges in stationary storage and building codes, and quickly gaining traction in the EV field. While propagation has long been a part of EV battery development, several global and international regulations are codifying Thermal Propagation as mandatory requirement. This talk focuses on the implementation in UN 38.3/ Dangerous Goods regulations and UNECE R100/E-marking requirements for vehicles.
-
Explore R100 Rev 3 Thermal Propagation requirements
-
Discover UN 38.3 T9-T13 test development and classification
-
Understanding the core methodology and criteria
-
Discuss timelines for implementation

Optimized Battery Controls For Vehicle Level Performance
Moderator:
Panelists: Praveen Chavannavar, Engineering Group Leader – NextGen Controls, General Motors
This round table event will convene experts from electric vehicle (EV) OEMs, battery manufacturers, and leading engineering consulting firms to explore the critical role of optimized battery controls in enhancing vehicle-level performance. As the EV market continues to grow, the need for sophisticated battery management systems that maximize efficiency, safety, and performance is more important than ever. This panel will delve into the latest advancements in battery control technologies, address integration challenges, and highlight collaborative opportunities across the industry to drive innovation.
Understand the Role of Advanced Battery Control Systems in Enhancing EV Performance: Gain insights into how state-of-the-art battery management and control systems impact vehicle efficiency, range, and overall performance, and learn about emerging strategies to optimize these controls for specific vehicle applications.
Explore Integration Challenges and Solutions Across Vehicle Subsystems: Discover the complexities involved in integrating battery controls with other vehicle systems, such as thermal management, power electronics, and propulsion, and learn about engineering approaches and best practices for achieving optimal system integration.
Identify Opportunities for Collaboration and Innovation Among Stakeholders: Discuss how OEMs, battery manufacturers, and engineering consulting firms can work together through joint projects, data sharing, and standardization initiatives to advance battery control technologies and drive the next wave of innovation in the electric vehicle industry.

Network Lunch Break
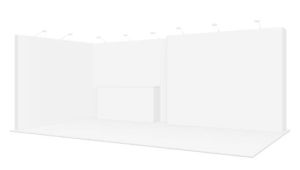

Optimizing EV Battery Pack And Cell Connection Systems: Overcoming Sensor Integration Challenges
The heart of an electric vehicle (EV) is its battery pack, with the cell connection system being crucial for both performance and safety. Integrating advanced sensor technologies into these systems is essential for monitoring critical parameters such as temperature, voltage, current, gas emissions, and water intrusion. This presentation explores the challenges and solutions in sensor integration for EV battery packs, focusing on how to enhance performance, safety, and longevity through precise and effective sensor deployment.
Understanding the Role of Temperature Sensors:
-
Learn how temperature sensors manage thermal conditions to prevent overheating and ensure optimal battery performance
-
Understand the impact of temperature fluctuations on battery health and safety, including risks like thermal runaway and lithium dendrite growth
Voltage and Current Monitoring Challenges:
-
Discover the importance of accurate voltage and current measurements in maintaining state of charge (SOC) and state of health (SOH) of battery cells
-
Explore the design requirements for sensor circuits to handle the dynamic stresses of charging and discharging cycles
Gas Detection and Water Intrusion Prevention:
-
Examine the critical role of gas sensors in early detection of thermal runaway and the types of gasses indicative of this condition
-
Learn about the challenges of detecting and mitigating water intrusion and coolant leaks to prevent short circuits and corrosion within the battery pack

Overcoming Challenges In EV Battery Module Welding: Speed And Precision With Lasers
With the rapid expansion of the electric vehicle (EV) industry, the demand for efficient and precise battery welding solutions is greater than ever. This presentation delves into advanced laser welding cell, which integrate cutting-edge technologies such as SCARA robots, dynamic clamping tools, and in-process monitoring. Designed to produce battery modules at an unparalleled speed of one module per minute, this automated solution addresses key challenges in the EV battery manufacturing process, ensuring high-quality welds and robust performance.
Understanding Remote Laser Welding Technology:
-
Learn about the capabilities of remote laser welding heads, including precision control and optimal penetration depth for high-quality welds
-
Explore how the integration of optical fibers and gantry systems enhances the welding process for various battery module configurations
Maximizing Efficiency with Dynamic Clamping and Vision Systems:
-
Discover the role of SCARA robots in applying precise pressure for consistent weld quality and how vision systems ensure accurate positioning of battery cells
-
Understand how dynamic clamping tools and real-time vision analysis contribute to achieving rapid welding cycles and minimizing downtime
Ensuring Quality and Safety with Advanced Monitoring and Fume Extraction:
-
Examine the importance of in-process monitoring systems for real-time validation of weld quality and the automatic detection of defects
-
Learn about the critical role of fume extraction systems in maintaining a clean work environment and preventing contamination that could affect weld integrity and safety

Streamlining EV Battery Manufacturing: The Role Of Electrode-Fixing Tapes
This presentation will introduce cutting-edge electrode-fixing tapes designed specifically for electric vehicle (EV) battery assembly. These tapes, manufactured in the USA, are engineered to enhance the safety, efficiency, and assembly process of EV batteries while ensuring compliance with industry regulations. Featuring electrolyte-compatible acrylic adhesives and distinctive green coloring, these tapes offer self-wound, liner-less construction for ease of use. Join us as we explore the innovative features and applications of these electrode-fixing tapes in optimizing EV battery design and assembly.
Understanding the Role of Electrode-Fixing Tapes in EV Battery Assembly:
-
Gain insights into the specialized adhesive properties and construction of electrode-fixing tapes used to bind multilayer electrode constructions in EV battery cells
-
Explore the significance of electrode-fixing tapes in optimizing the structural integrity and performance of EV battery components
Exploring the Benefits and Features of Electrode-Fixing Tapes:
-
Learn about the electrolyte-compatible acrylic adhesives and highly visible green color of these electrode-fixing tapes, enhancing safety and visibility during assembly
-
Understand the advantages of self-wound, liner-less construction and the availability of various widths on plastic cores for efficient application in EV battery manufacturing
Addressing Key Challenges in EV Battery Manufacturing:
-
Discover how electrode-fixing tapes contribute to reducing flammability, boosting dielectric strength, and optimizing design and assembly processes in EV battery manufacturing
-
Explore the role of polyethylene terephthalate (PET) and polypropylene (PP) plastic facestocks in ensuring chemical inertness and preventing self-discharge in EV battery cells

Prioritizing Safety: Navigating EV Battery Testing Challenges
As electric vehicle (EV) batteries evolve with increased energy capacity and power output, ensuring personnel safety during testing becomes paramount. This presentation offers an in-depth exploration of critical safety considerations for personnel and test setups in EV battery testing. From facility requirements to specialized equipment and proactive/reactive safety measures, attendees will gain valuable insights into maintaining safety while handling high-voltage electronics and batteries. Through case studies and best practices, this session emphasizes the importance of prioritizing safety in EV battery testing to ensure a secure and promising future for EV technology.
Understanding Safety Requirements in EV Battery Testing:
-
Explore the evolving challenges posed by the increasing energy capacity, power output, and recharge speeds of EV batteries
-
Learn about the essential safety protocols and facility requirements necessary to mitigate risks during EV battery testing
Exploring Specialized Test Equipment and Real-Time Monitoring Solutions:
-
Gain insights into the specialized test equipment and real-time monitoring systems used to ensure personnel safety and data integrity during EV battery testing
-
Understand the role of advanced technologies in detecting and responding to potential safety hazards in real-time
Implementing Proactive and Reactive Safety Measures:
-
Discover proactive safety measures aimed at preventing accidents and minimizing risks before they occur during EV battery testing
-
Learn about reactive safety measures designed to swiftly address safety incidents and protect personnel and equipment in emergency situations

Safeguarding The Future: Battling Particle Contamination In EV Battery Manufacturing
As the electric vehicle (EV) industry surges forward, the safe and efficient production of EV batteries becomes increasingly vital. However, an often overlooked challenge in this process is particle contamination, which can jeopardize safety, performance, and efficiency. This presentation delves into the implications of particle contamination in EV battery manufacturing and explores innovative solutions to address this issue. From understanding the risks associated with particle contamination to implementing advanced detection technologies and setting contamination baselines, attendees will gain insights into safeguarding EV battery production. Additionally, the presentation highlights the critical role of particle counting in recycling end-of-life EV batteries to ensure environmental sustainability and economic viability.
Understanding the Risks of Particle Contamination:
-
Explore the safety hazards posed by particle contamination in EV batteries, including risks of short circuits, thermal runaway, and compromised performance
-
Recognize the challenges faced by fire crews in extinguishing EV battery fires due to their unique characteristics.
Challenges in Particle Detection and Inspection:
-
Learn about the limitations of traditional inspection methods for detecting particles in EV battery cells and the need for scalable next-generation solutions
-
Explore innovative approaches such as automated inspection systems and advanced imaging techniques to enhance particle detection capabilities
Implementing Contamination Control Measures:
-
Discover stringent contamination control measures and advanced detection technologies employed to mitigate hazards and uphold production quality
-
Understand the distinction between conductive and non-conductive particles and their respective impacts on battery performance
Recycling and Repurposing End-of-Life Batteries:
-
Recognize the urgency and importance of recycling end-of-life EV batteries to recover valuable materials, minimize environmental impact, and harness economic potential
-
Explore the role of particle counting in ensuring the safety, performance, and environmental sustainability of repurposed battery systems

Breaking Boundaries In EV Battery Assembly: The Lamination Revolution
Explore the cutting-edge advancements in EV battery module assembly with the introduction of an innovative cell contacting system (CCS) lamination approach. This transformative method eliminates the need for traditional positioning methods like molded plastic trays and foams, offering enhanced precision, flexibility, and sustainability. Discover how rigorous testing and qualification of PET insulation foils and adhesives from multiple suppliers have streamlined CCS design and assembly, driving efficiency and reducing environmental footprint. With a focus on sustainability and efficiency, this groundbreaking approach is poised to shape the future of EV battery module design and assembly.
-
Understanding the Limitations of Traditional CCS Assembly Methods: Explore challenges posed by conventional methods such as molded plastic trays and foams in CCS assembly, including weight, complexity, and structural limitations
-
Introduction to Advanced Lamination Approach: Learn about innovative hot and cold lamination processes designed to eliminate the need for traditional positioning methods and offer enhanced precision and flexibility
-
Qualification of PET Foils and Adhesives: Discover how rigorous testing and qualification of PET insulation foils and adhesives have streamlined CCS design and assembly
-
Implications and Benefits of Advanced Lamination Approach: Understand the far-reaching implications of this approach, including improved structural integrity and lifespan of EV battery modules, reduced manufacturing cycle times, and environmental footprint
-
Focus on Sustainability and Efficiency: Explore the commitment to sustainability and efficiency through the reduction or elimination of traditional adhesives, addressing concerns over longevity, environmental impact, and manufacturing efficiency

Afternoon Networking Break
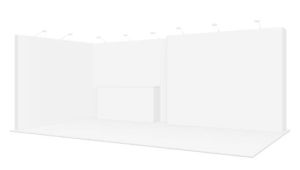

Revolutionizing Recycling: Pioneering Designs For Intrinsic Recyclability In Electrodes And Cells
Explore the frontier of battery recycling with our presentation, “Revolutionizing Recycling.” We’ll delve into ground-breaking designs aimed at embedding recyclability directly into electrode and cell structures. Attendees will uncover the challenges and opportunities inherent in pioneering intrinsic recyclability, from material selection to manufacturing processes. Throughout the session, insights into innovative design principles, regulatory considerations, and collaborative strategies will be shared, empowering participants to drive meaningful change in the battery industry. By the conclusion, attendees will be equipped with strategies to revolutionize recycling practices, minimize waste, and foster sustainability in battery technology.
-
Explore ground-breaking designs aimed at embedding recyclability directly into electrode and cell structures
-
Uncover challenges and opportunities inherent in pioneering intrinsic recyclability, from material selection to manufacturing processes
-
Gain insights into innovative design principles, regulatory considerations, and collaborative strategies to drive meaningful change in the battery industry towards sustainability

40 Min Round Table Panel Discussion
Powering The Future: The Role Of Solid-State Batteries In The US EV Market
Moderator:
Panelists:
The electric vehicle (EV) revolution is transforming the automotive industry, with the US playing a pivotal role in this global shift. As the demand for more efficient and safer battery technologies grows, solid-state batteries are emerging as a key innovation. This round table discussion will delve into the advancements in solid-state battery technology, the challenges the US faces in securing critical minerals, and the strategic efforts to establish a robust supply chain. By examining the intersection of technology, geopolitics, and industry strategy, we will explore how the US can maintain its competitive edge in the EV market.
Understand Solid-State Battery Technology:
-
Gain insights into the advancements and benefits of solid-state batteries, including their higher energy density, improved safety, and potential to revolutionize the EV market
-
Explore the current state of solid-state battery research and development in the US, including key players and emerging trends
Analyze the Geopolitical and Economic Challenges:
-
Examine the US’s efforts to secure critical minerals essential for solid-state battery production amid global competition and geopolitical tensions
-
Understand the impact of the Inflation Reduction Act of 2022 and other policies on the US EV supply chain and how they aim to reduce dependence on foreign sources
Explore Strategic Industry Initiatives:
-
Investigate the initiatives and partnerships the US is fostering to build a resilient and sustainable EV battery supply chain, including collaborations with tech startups and academic institutions
-
Assess the potential of battery recycling and other innovative solutions to address raw material shortages and ensure long-term supply chain security

Maximizing Output, Minimizing Waste: Approaches To Effective Black Mass Chemical Treatment
Join us for an in-depth exploration of effective chemical treatment methods for black mass in battery recycling operations. Our presentation focuses on maximizing output and minimizing waste through innovative approaches to black mass treatment. Attendees will gain insights into the challenges and opportunities associated with chemical treatment techniques, including material recovery, process optimization, and environmental considerations. By the end of the session, participants will be equipped with actionable strategies to enhance the efficiency and sustainability of black mass treatment processes, driving positive environmental impact and economic growth in battery recycling operations.
-
Effective Chemical Treatment Methods for Black Mass: Explore innovative approaches to chemical treatment for black mass in battery recycling operations
-
Maximizing Output and Minimizing Waste: Understand strategies to maximize output and minimize waste through effective black mass treatment techniques
-
Actionable Strategies for Efficiency and Sustainability: Gain insights into actionable strategies for enhancing the efficiency and sustainability of black mass treatment processes, driving positive environmental impact and economic growth in battery recycling operations

Towards Eco-Friendly Batteries: Redefining Sustainability In Design And Recycling
In our presentation, “Towards Eco-Friendly Batteries,” we explore the paradigm shift in battery sustainability through innovative design and recycling practices. Attendees will delve into the challenges and opportunities inherent in redefining sustainability across the battery lifecycle, from initial design to end-of-life recycling. Throughout the session, insights into eco-friendly material selection, manufacturing processes, and circular economy principles will be shared, empowering participants to drive meaningful change in the battery industry. By the conclusion, attendees will be equipped with strategies to enhance sustainability, minimize environmental impact, and foster a greener future for battery technology.
-
Explore challenges and opportunities in redefining sustainability across the battery lifecycle
-
Learn about innovative design and recycling practices aimed at minimizing environmental impact
-
Gain insights into sustainable material selection and manufacturing processes for batteries
-
Understand the importance of adopting eco-friendly practices to reduce resource consumption and waste generation
-
Explore circular economy principles and their application in battery design and recycling
-
Learn strategies to enhance sustainability and promote a greener future by adopting circular economy practices in the battery industry

Chairs Closing Remarks
